After reading this article, you will understand the process of fabric dyeing
- Share
- Issue Time
- Nov 20,2024
Summary
Fabric dyeing is an indispensable process in the textile industry. It not only affects the aesthetic quality of the finished product but also directly relates to its overall quality and market competitiveness. The entire fabric dyeing process can be divided into five main stages: preparation, dyeing, post-treatment, quality inspection, and packaging and storage. These interlinked stages form a systematic dyeing procedure.
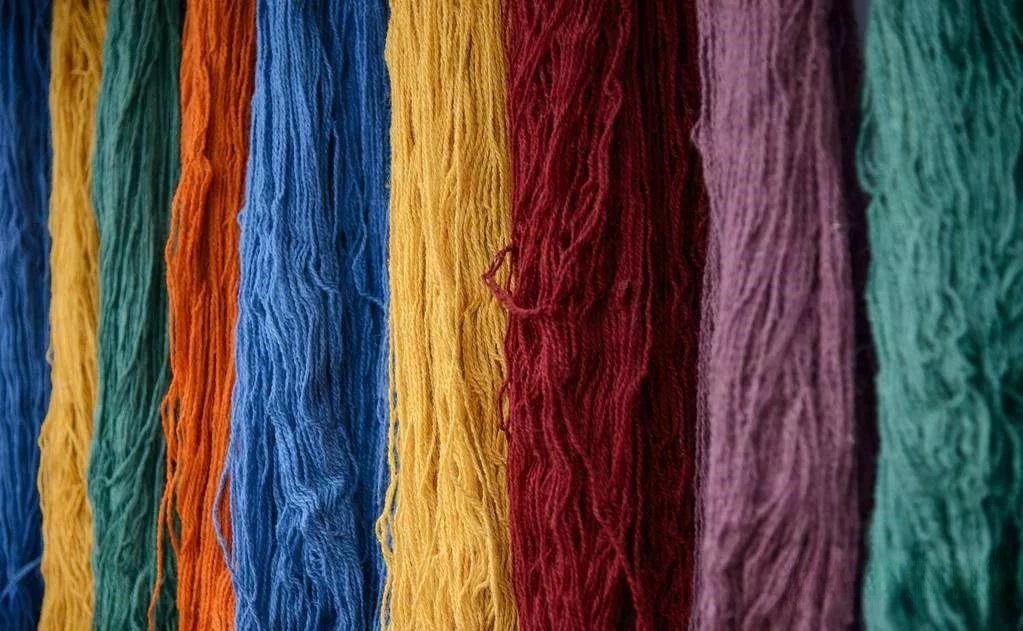
After reading this article, you will understand the process of fabric dyeing
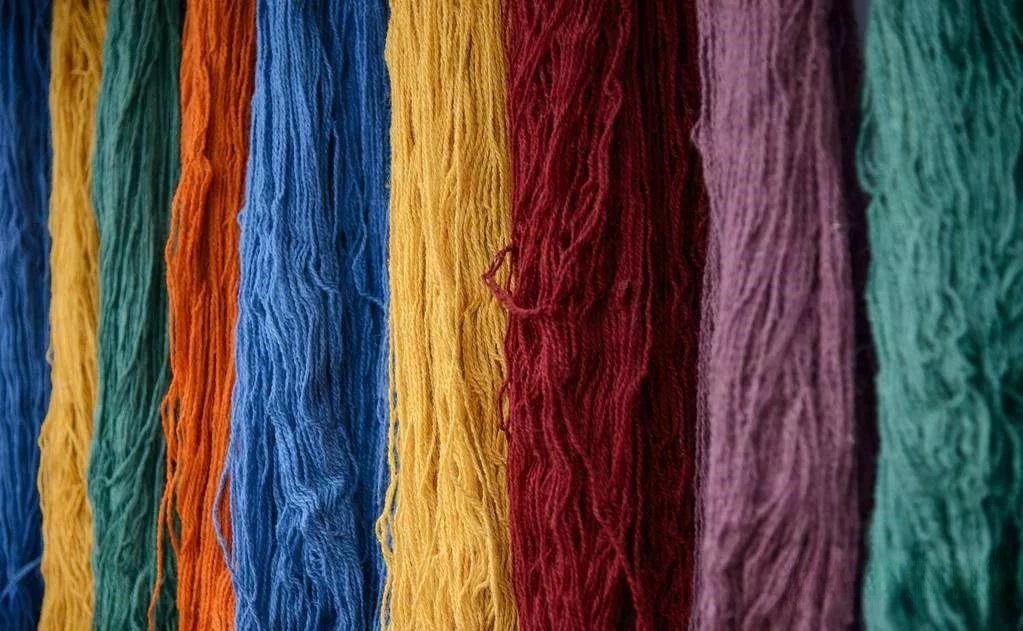
Fabric dyeing is an indispensable process in the textile industry. It not only affects the aesthetic quality of the finished product but also directly relates to its overall quality and market competitiveness. The entire fabric dyeing process can be divided into five main stages: preparation, dyeing, post-treatment, quality inspection, and packaging and storage. These interlinked stages form a systematic dyeing procedure.
Firstly, in the preparation phase, the cleaning and conditioning of the fabric are crucial. The primary goal during this stage is to ensure that the fabric is in optimal condition before dyeing. Typically, newly purchased fabrics carry oils, dust, and other impurities, which can affect the uniformity and effectiveness of the subsequent dyeing process. Therefore, the fabric needs to undergo pre-treatment steps, including soaking, washing, and stain removal, to eliminate surface contaminants. In addition to cleaning, pre-shrinking is another significant step in the preparation process. This involves using heat and moisture to shrink the fabric beforehand, thereby reducing potential unevenness after dyeing. Furthermore, selecting appropriate detergents and treatment methods according to the specific characteristics of the fabric is critical to avoid damaging the material.
Next is the dyeing stage, which is the most critical part of the entire process. During this phase, selecting the right dye and dyeing method is very important. The type of dye used will vary depending on the fabric material; for example, reactive dyes are commonly used for natural fibers like cotton and linen, while disperse dyes are more suitable for synthetic fibers like polyester. The dyeing methods include various forms such as batch dyeing, continuous dyeing, and spraying, each having its unique application scenarios and effects. Key parameters such as temperature, time, and pH levels must be strictly controlled to ensure that the dye penetrates and bonds with the fabric effectively, achieving the desired color depth and shade. Additionally, monitoring the concentration and temperature of the dye bath throughout the dyeing process is vital for the final outcome.
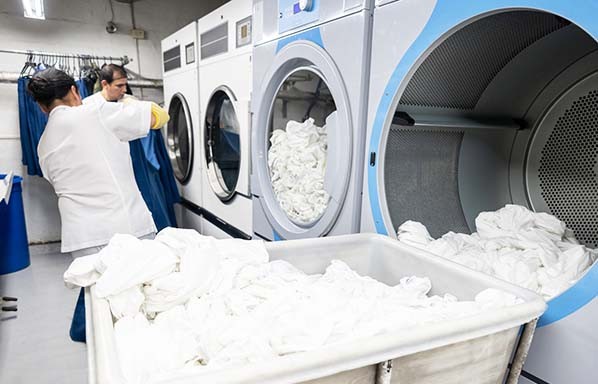
After dyeing is completed, the fabric moves into the post-treatment phase, where the primary tasks are fixing the dye and enhancing the fabric's durability. Post-treatment steps usually include washing, acid-base treatment, and softening. The purpose of washing is to remove any unbound dye to prevent fading in subsequent uses. Acid-base treatment can improve the binding strength of the dye and enhance color fastness, helping the fabric maintain its color stability during washing and everyday use. Softening treatments aim to improve the hand feel of the fabric, making it softer and more comfortable. These post-treatment processes significantly enhance the quality of the finished product, making the fabric more competitive in the market.
Subsequently, the fabric enters the quality inspection phase. After dyeing and post-treatment, a comprehensive quality check is necessary to ensure compliance with preset standards. Quality control is typically conducted by trained inspectors who evaluate the fabric's color consistency, color fastness, hand feel, and appearance. Methods for quality inspection include laboratory testing, color difference measurement, and on-site random sampling. Only through rigorous quality checks can the reliability of the finished product be ensured, avoiding customer complaints and returns due to substandard quality.
Finally, once the quality inspection is complete, the fabric moves into the packaging and storage phase. In this stage, the fabric is organized, folded, and properly packaged for transport and sale. Packaging usually includes relevant quality inspection reports for customer reference. This not only enhances consumer trust but also helps the company establish a good brand image in the market. Additionally, effective inventory management and storage conditions are key to ensuring fabric quality, preventing degradation due to moisture, direct sunlight, or other adverse factors during storage.
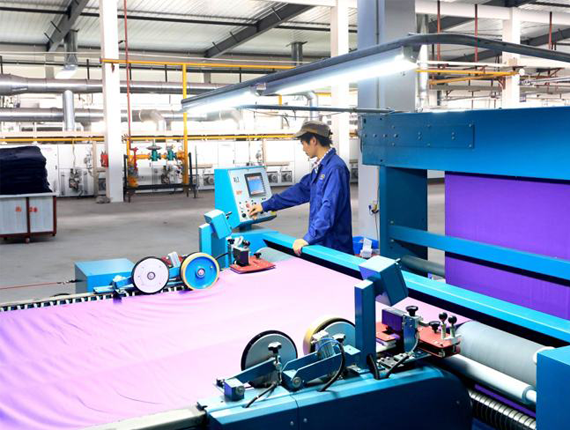
In summary, the overall process of fabric dyeing encompasses multiple stages from preparation to packaging, with each step playing a crucial role in determining the quality and appearance of the final product. As technology advances, dyeing processes are continuously innovating, with environmentally friendly and efficient dyeing methods gradually becoming new trends in the industry. By continually optimizing and improving these processes, fabric dyeing techniques will become more sophisticated, meeting the increasingly diverse demands of the market.